Case Study Betagran Lipezk LLC
Requirements:
- Reproducible growth conditions
- Low risk of contamination
- Optimal growth of cell cultures
- High process reliability
BINDER solutions:
- Reliable decontamination concept
- High level of temperature uniformity
- VENTAIR air jacket system
- High relative humidity of up to 95% RH
- Stable pH values thanks to driftfree CO2/O2 IR sensor technology
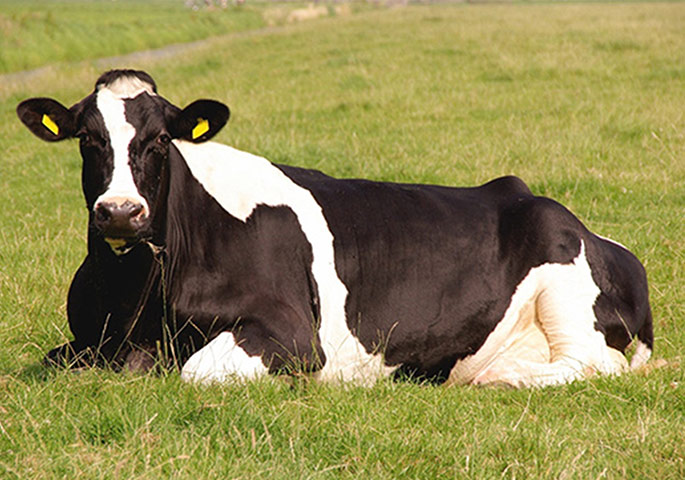
Russian company Betagran Lipezk LLC produces cattle embryos for accelerated herd breeding
Schelkovo Agrohim JSC holds a leading position on the Russian market in the manufacturing and distribution of plant protection products. The company’s focus is on manufacturing pesticides that provide full-coverage protection for the most important agricultural crops, as well as agrochemicals containing micronutrients for controlling the supply of minerals to plants. One of its latest ventures is in dairy cattle breeding, and at the end of 2014, it opened a stateof-the-art facility designed for this purpose: Betagran Lipezk LLC. Where the facility’s expertise lies is in producing cattle embryos for accelerated breeding of dairy and meat herds. Its primary aim is to produce embryos from genetically high-quality breeds of cattle in order to sell them on to breeding-industry companies, creating a core breeding stock and improving the genetic characteristics of herds in the process. Total investment in the project – the only one of its kind in Russia – has amounted to 370 million rubles (more than 6 million US dollars).
Producing embryos involves fertilizing the highquality oocytes obtained from elite breeds of cattle, then growing them in vitro to the point at which they become mature embryos. These embryos are then cryopreserved, a process that uses low temperatures, and stored until they are applied in embryo transfer technologies further down the line. The elite embryos can be stored in liquid nitrogen at temperatures of as low as -196°С for an unlimited period of time, as these conditions preserve their vitality. When it comes to working with embryos, sterile conditions and maximum process reliability are of the utmost importance. This is exactly why Betagran Lipezk LLC made the decision to use CO2 incubators from BINDER’s CB series in order to produce mature embryos. These incubators feature an innovative safety concept: Hot-air sterilization at 180°C is performed regularly, ensuring the unit provides a completely sterile environment for embryo growth. One of the main elements in the unit is a fixed, heatsterilizable CO2 sensor. “Working with mammalian cells involves a high risk of external contamination”, says biotechnologist Nikolay Chromov, who is responsible for the project at Betagran Lipezk LLC. “We need to operate in line with regulations and record our activities, ensuring that we maintain the strictest standards of sterility in the area in which we are working and in our processes. That is why we opted for BINDER incubators: Thanks to the auto-sterilization with hot air they provide, there is virtually no chance of contamination occurring.”
As the cells are highly sensitive to environmental conditions, it is essential that growth conditions are kept constant and reproducible in order to make cultivation as effective as possible. “Cultivating embryos requires us to keep all the parameters – such as temperature, humidity, and gas composition – at precise levels. The BINDER units are unsurpassed in their reliability and create entirely constant incubation conditions”, says Nikolay Chromov. “Separate doors make it possible to rule out significant changes in the atmosphere within the unit during work with individual plates.”
The specialist is thrilled with the way in which the unit parameters are quickly restored: “If a door is opened or a gas cylinder is changed, the parameters return totheir original values extremely quickly – so there is no harmful impact on the cells.” Thanks to a BINDER VENTAIR® air jacket system, the temperature is also distributed homogeneously across all levels. Together with the double-pan humidifying system and condensation protection, the air jacket system ensures that the incubator is kept free from condensation. The high level of humidity in the incubator atmosphere effectively prevents nutrients from evaporating. “We are extremely pleased with the BINDER incubators. We are
planning to expand the facility in the near future, and would love to add more BINDER incubators in different sizes for use in our in vitro technologies”, says Nikolay Chromov.
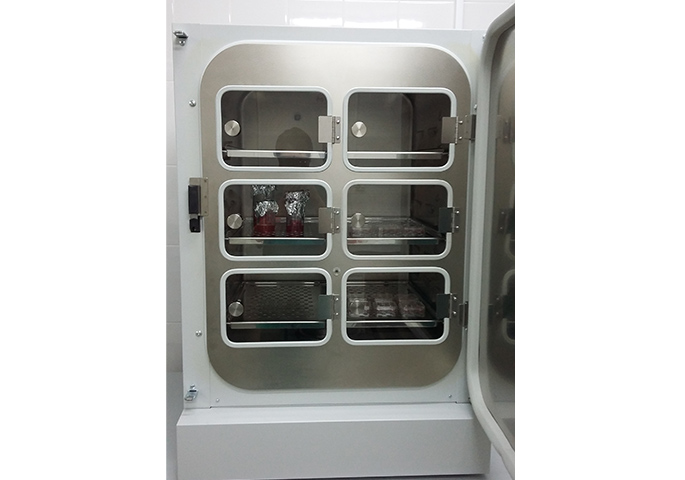
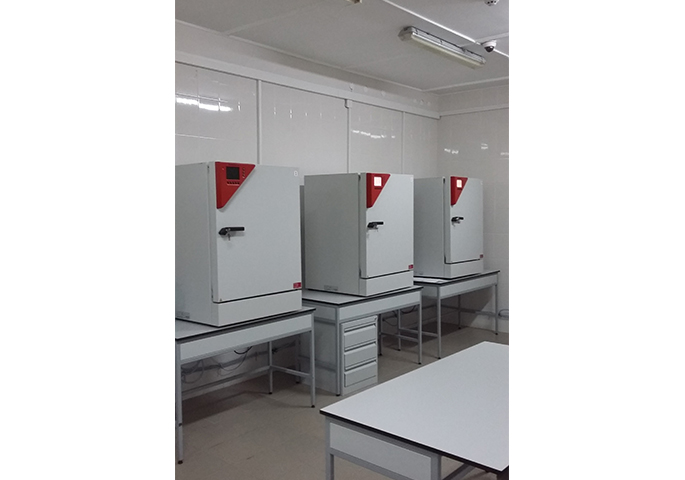
Advantages:
- Auto-sterilization with hot air at 180 °C
- CO₂ gas-mixing jet with Venturi effect
- Tightly-sealed inner door made of tempered safety glass
- Seamless, deep-drawn inner stainless steel chamber