Case study: Incubator for automated microbiological tests
Customized BINDER solution
In the pharmaceutical and food industries, microbiological quality control is essential in ensuring product safety and quality. Our customer is developing technologies that make it possible to detect microbial contamination more quickly in the manufacture of pharmaceuticals, care products and medical technology instruments and would like to implement this microbial quality control process in an automated system. The aim is to make microbiological tests more efficient and reliable in order to reduce the workload and prevent inconsistencies. At the heart of such an automated system for microbial quality control is the incubator. In close consultation with the customer, BINDER Automation & Integrated Solutions designed and developed a customized incubator specifically for this system, which meets the specific requirements and can be seamlessly integrated into the system.
The requirements:
- Temperature stability at 22.5°C or 32.5°C
- High cooling capacity and heat compensation
- It must be possible to compensate for the heat input of the electronically controlled carousel and the robotics used to transport the Petri dishes
- Sophisticated air circulation: hotel taken into account, as it takes up the majority of the incubator interior
- Design of a mechanical interface to the customer system that ensures an optimum supply of fresh air for the Peltier elements in the incubator
- Provision of system parameters to the customer system (software interface)
- Door mechanism that enables the incubator to be installed in the overall system and is also easy to service
Our services:
- Formation of a project team consisting of a technical project manager, a product manager and engineers from the fields of mechanics, software and systems
- Coordination with the customer regarding interfaces (hardware and software) and system requirements
- Suggestions on how best to implement the interfaces in the customer system
- Performance of air flow simulations to ensure optimum spatial and temporal temperature stability
- Validation and verification of units
- Preparation of the requirements and functional specifications
- Provision of prototypes for functionality testing in the overall system
- Technical product documentation
- Service training for the customer
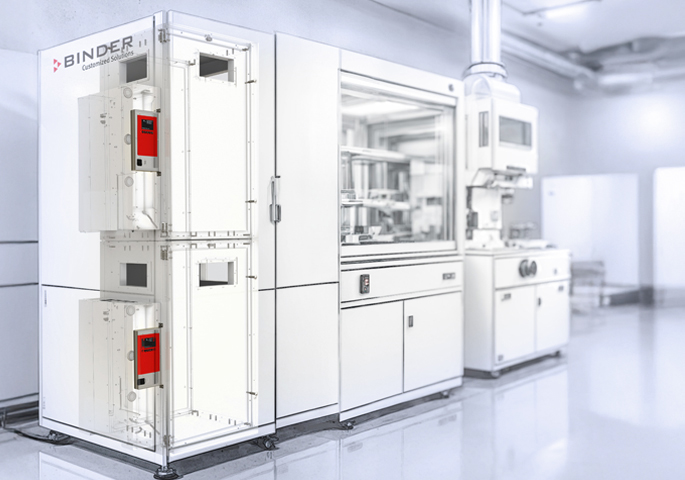
The BINDER solution:
- Two incubators with a lateral “rucksack” for power electronics that meet the requirements
- Technical data of incubator (empty):
- Temperature range: 20 – 35°C
- Temperature fluctuation: 0.3 K at 32.5°C
- Temperature uniformity: 1.5K at 32.5°C
- Max. heat compensation at 32.5°C: 130W
- Energy consumption at 32.5°C: 50 Wh/h
- Mechanical interface to the customer system with specially designed air duct with integrated external fans to ensure the necessary fresh air supply for the Peltier elements
- Sophisticated air circulation within the incubator by way of computer simulation, taking into account the limitations of the carousel installed by the customer
- Communication interface to the customer system via ModBus TCP
- Practical screw cap for the door that ensures optimum installation in the customer’s system and is also easy to service