Case Study Emil Frei Gmbh & Co. KG
Tasks:
- Dry coatings in a short time at a high temperature
- Consistent temperature distribution
- Door easy to open
- Chemical resistance tests
- Complete reliability for applications that use solvents
BINDER solutions:
- FDL 115 safety drying chambers
- Temperature range: ambient temperature plus 300 degrees
- Controller with time-segment and real-time programming
- Fresh-air monitoring with audible and visual alarm and automatic deactivation of heating
- Replaceable fresh-air filter cartridge, Class M6 spare filter according to DIN EN 779:2012
- Class 2 independent adjustable temperature safety device (DIN 12880) with visual alarm
- Computer interface: RS 422
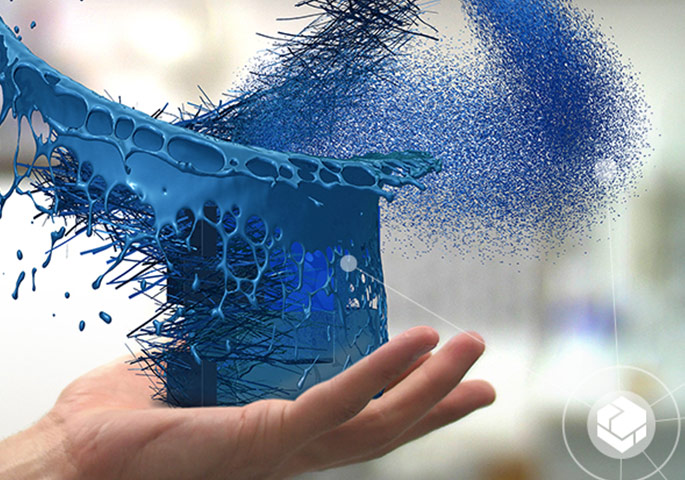
FreiLacke, based in the town of Döggingen in Germany’s Black Forest, manufactures over 18,000 different coating formulations. Employing 550 people, it is known as the leading supplier of system coating solutions within the markets on which it focuses. So just what is it that leads so many customers to choose FreiLacke?
Service staff member Rüdiger Oschwald has the answer: “Our product range contains more coating systems than almost any other company. In some applications, it’s really important for customers to get all their coatings from the same source, so they can be sure the shades will match up perfectly. Wheels in the automotive industry are a good example, as they have a layer of powder coating applied to them, then a liquid coating and another layer of powder coating.” To ensure that its coatings are doing their job of making items more durable and visually appealing, as well as adding value to them, FreiLacke puts the quality of its products to the test on a neardaily basis. That’s where employees like Reinhold Weißer, Rüdiger Oschwald, and Ronny Buck come in. They perform these tests using 30 different BINDER chambers. Ronny Buck, who is responsible for development and application technology in the area of industrial coatings, uses two FDL safety drying chambers for investigating solvent-based coatings and gaining new insights into these materials. As a laboratory
technician, he finds BINDER chambers a real pleasure to work with because the DIN A2-sized test panels that he uses fit precisely inside them. His day of testing kicks off as early as six o’clock in the morning, with the safety drying chamber then running uninterrupted for a full twelve hours.
A panel that has been coated with a solvent-based material normally takes an hour to dry at 70 degrees. “Anything that separates out of the solvent is extracted during the drying process, and the waste heat is also fed back into the heating system, which helps us save energy,” says Buck. BINDER’s safety drying chambers prevent anything from disrupting the process of drying solvent-based coatings. “I’m absolutely delighted with our BINDER chambers. We can take the prepared test panels to our customers and show them what the color of the coating looks like when it’s dry, or how the surface feels, for instance,” Buck explains. For Oschwald, chemical resistance tests are also crucial: These test how coatings behave when they come into contact with other materials such as cooling lubricant or grease. Once it has been coated, the test panel is placed in a vessel containing a certain substance and is then exposed to a temperature of some 80 degrees. This is a long-term test that takes more than a month.
There are also special tests that the coatings undergo, the latest of which involves a segment of an alloy wheel. In this case, the segment has been sitting in a safety drying chamber for 14 days so far and will continue to be exposed to sources of stress for some time to come. Oschwald and his team perform all manner of tests like these every day and can speak from their experience with BINDER chambers:
“They’re durable, they’re reliable, and they deliver accurate temperatures.”
FreiLacke also manufactures powder coatings, which are much in demand the world over. These materials do not use any solvents at all and are also applied to panels for testing purposes. FreiLacke uses several BINDER drying and heating chambers (FED 115) for this purpose: The powder coating on the test panels is placed in the oven, where it is melted by the heat and then forms a chemical bond. This is just one more example of how versatile BINDER chambers are – and how there is a BINDER chamber to suit virtually any application.
Advantages of safety drying chambers
- Fulfill the safety requirements of EN 1539:2010-08
- Short drying times due to high temperature accuracy and defined ventilation
- Interior free from silicone and dust
- Easily replaceable fresh-air cartridge ensures constant fresh-air quality
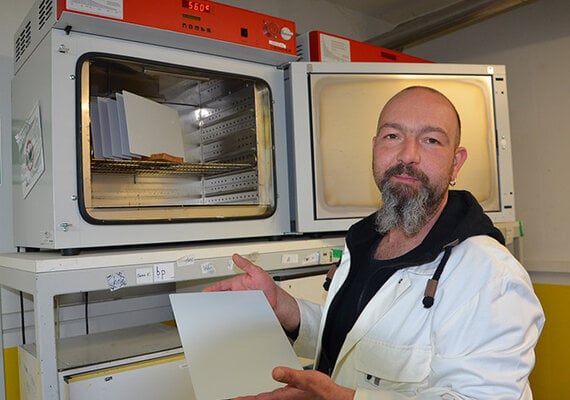